We recently spoke with Vandana Mathur, Supervisor of Transportation Mobility & Research at NJDOT, to learn more about the agency’s ongoing innovative mobility and operations initiatives. The discussion navigated advancements such as enhanced IMR truck equipment for safer incident response, real-time weather monitoring through the Weather Savvy program, and smart truck parking technology to address parking space shortages. These efforts reflect NJDOT’s commitment to using data-driven, next-generation solutions to improve roadway safety and efficiency across the state.
Q. Can you tell us about the initiative to equip NJDOT Incident Management Response (IMR) trucks with lighting towers and LED flares at incident scenes as part of the EDC-7 Next-Generation TIM – Technology for Saving Lives?
A. NJDOT secured funding from the Federal Highway Administration (FHWA) to enhance its Incident Management Response (IMR) trucks by equipping them with light towers and LED flares. This initiative has already significantly improved NJDOT’s on-scene operational capabilities—particularly in low-light conditions—by increasing both safety and efficiency. The light towers provide critical illumination, enabling first responders to better assess the scene, identify debris, and evaluate the extent of the crash. The improved visibility also enhances personnel safety by alerting approaching drivers to the presence of an emergency scene, giving them time to slow down and avoid secondary incidents.
Unlike traditional emergency lights, which can be blinding, the LED flares equipped on NJDOT’s IMR trucks use a calmer, sequential lighting pattern that is less jarring to drivers while still maintaining a strong visual presence. The light towers provide wide-area illumination that surpasses the limited reach of standard vehicle emergency lights, ensuring that all personnel working at the scene are clearly visible. Designed for quick deployment, the towers deliver lighting rapidly when it’s most needed.
This initiative plays a critical role in supporting Traffic Incident Management (TIM) by enhancing the safety for both emergency responders and drivers during roadway incidents.
Q. You mentioned the benefits of the lighting towers and LED flares compared to traditional flashing lights – are emergency responders moving away from using flashing lights altogether? Additionally, have they been installed and implemented into all NJDOT IMR trucks or is this an ongoing process?
A. Yes, we often use the new tools instead of the flashing lights, especially because they can be deployed immediately. We have installed the lighting towers and LED flares on 22 IMR trucks across the state. These tools are used frequently—on average, once per week or several times per month—which shows they’re a valuable and necessary source for incident management. Because they have proven so effective, it is now standard practice to include light towers and LED flares on all new IMR trucks added to the fleet.
Q. Staying on TIM, can you describe the Drivewyze alert project? How does it collect and distribute data, and what are some potential benefits?
A. Drivewyze is a product that we are purchasing through the University of Maryland as part of the Transportation Data Marketplace (TDM) and the Eastern Transportation Coalition, which benefits New Jersey and the 19 other coalition member states. Drivewyze sends safety alerts to commercial vehicles’ Electronic Logging Devices (ELDs)—which all truckers have—and since the alerts are free, both drivers and fleet operators can sign up to receive them.
The system generates alerts using INRIX data and provides warnings for low bridges, high rollover zones, weight restrictions, “no trucks in left lane” zones, and sudden slowdowns and congestion. Because commercial vehicles need more time to stop than passenger vehicles, due to their size and weight, timely slowdown warnings can be especially critical for safety.
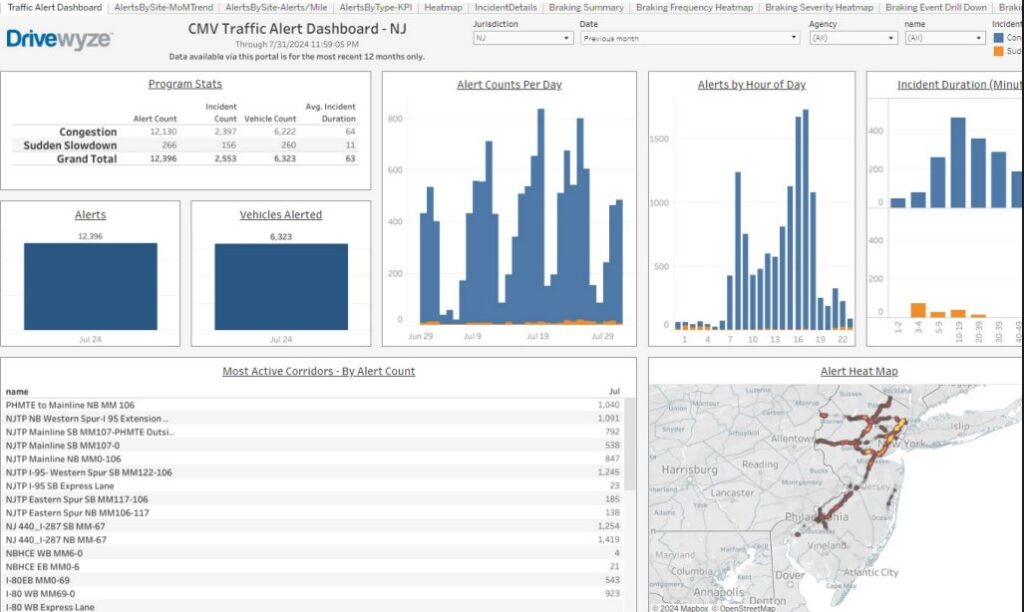
As part of its service, Drivewyze provided us with a dashboard that show the number of alerts sent, categorized by alert type. We use this data to assess performance. For example, by reviewing the number of alerts issued over the past three months, we evaluate whether alerts are being sent to the right places at the right times. When I joined the NJDOT team, I emphasized the importance of verifying and validating this data—not just accepting numbers that look good on paper.
We reached out to NJIT, our resource center, to help us conduct real-world testing during peak hours to confirm whether the alerts were actually reaching vehicles on the road. Initially, NJIT found that static alerts were working well, but congestion alerts were not coming through. When I contacted Drivewyze, they responded that they had forgotten to enable congestion alerts and said they had fixed the issue. NJIT conducted follow-up test runs in April to confirm the fix.
In the second round of testing, static alerts continued to perform well—NJIT even received a new static message related to a closure of Exit 34 due to a sinkhole. However, congestion alerts still underperformed. Despite driving through 83 congestion zones at speeds under 25 mph, NJIT researchers only received 5 congestion alerts. We will continue working with Drivewyze to make sure this issue is fully resolved.
Q. Moving to a different topic, at the most recent NJ STIC meeting you mentioned recent advancements in the Weather Savvy pilot. What technologies are used in the Weather Savvy program, what benefits does it provide, and how has it evolved since it first began?
A. We launched the Weather Savvy pilot project in 2020 to gain real-time situational awareness of roadway conditions. We began by equipping 12 NJDOT vehicles with Vaisala MD30 weather sensors. These sensors collect a range of data such as air temperature, road surface temperature, grip levels, frost point, dew point, and whether the road surface is wet, icy, or dry. Each vehicle also contains tablets that display this information to the driver and relays it to a central server, administered by NJIT, via a wireless router installed in the vehicle. A road-facing camera mounted on the vehicle provides real-time video of roadway and weather conditions.
Since the project began, we have expanded from 12 to 45 NJDOT vehicles, including plow trucks, Safety Service Patrol (SSP) trucks, and operations supervisor pickup trucks. All collected data is accessible through a web portal developed by NJIT, which features a map showing each vehicle’s location, online/offline status, and travel history over the past 15 minutes. The portal also includes color-coded indicators for road surface conditions and allows users to click on specific locations for detailed information.
Last year, NJIT enhanced the portal by integrating additional roadside sensors, including Vaisala GroundCast and acoustic sensors. GroundCast is a battery-operated, in-pavement cylindrical sensor that collects data on surface, ground, and base temperatures, as well as the presence of roadway chemicals. The acoustic sensors record the sound of vehicles driving over the road and use an AI model to classify the road surface conditions. All of this data has been integrated into the Weather Savvy web portal to support better live monitoring of road conditions.
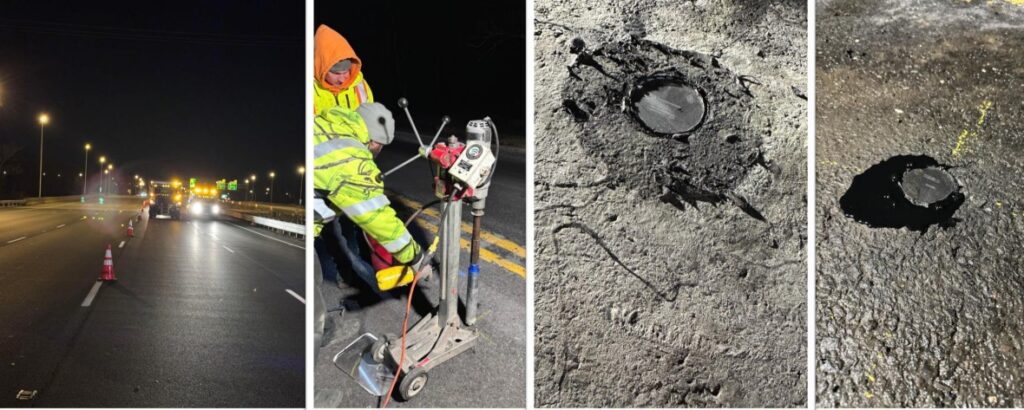
Right now, we are working toward integrating three sources of weather data: the mobile Weather Savvy vehicles, stationary road sensors across the state, and potential virtual Road Weather Information Systems (RWIS) data. Our goal is to merge all three sources to create the most accurate, real-time understanding of road and weather conditions. This phase is still in the early pilot stage.
Q. Is NJIT’s Weather Savvy web portal publicly accessible, or is it only shared with NJDOT?
A. Right now, the Weather Savvy web portal is internal-only, since it’s still a pilot project. We want to ensure that we have a solid, data-driven foundation before releasing any information to the public. That said, it has been really exciting to see how the data comes together. I have shared many images during STIC and other state meetings to give people a look at the portal. It is a very cool and innovative project. In fact, NJDOT, NJIT, and our technical partners from Vaisala and EAI won the 2021 “Outstanding Project Award” from the Intelligent Transportation Society of New Jersey (ITS-NJ) for Weather Savvy.
Q. During the previous STIC meeting, the Mobility and Operations team mentioned that you are testing direct streaming from sensors to servers on two of the Weather Savvy vehicles. Can you explain this initiative?
A. For the Weather Savvy project, one of the challenges we’ve faced is ensuring consistent data transmission from the trucks. Since drivers are inside the vehicles managing multiple devices—including laptops and tablets—there are times when the laptops shut off or something else interrupts the data flow. With a fleet of 45 trucks, keeping them all fully operational is a year-round task that keeps us constantly busy.
To address these issues, NJIT developed an API that allows the data to be sent directly to their server, bypassing the middle steps involving the tablet, laptop, and router. At first, they planned to roll this change out across the entire fleet, but I told them to start with a small test—just two trucks—to see how well the direct data transmission works. This change will also only apply to certain vehicles; for example, the IMR trucks will keep their tablets in place.
Q. Can you describe some of the technology used in the Truck Parking Pilot, what NJDOT has implemented so far, and some next steps for the future?
A. For the Truck Parking Pilot, we have deployed a range of technologies to better monitor and manage available spaces. First, we use in-pavement magneto-resistive sensors—referred to as “pucks”—manufactured by a company called Sensis Networks. These sensors detect whether a truck is occupying a particular space, and because truck parking spaces are so long, we have installed two pucks per space to ensure accurate detection. In addition to pucks, we installed traffic microwave sensors—one at the entrance and one at the exit of rest areas—to help us count the number of trucks entering and exiting each site. We also equipped the rest areas with CCTV cameras that provide live video feeds, supplementing the sensor data with visual information.
To transmit the collected data to NJIT servers, we use 4G and LTE modems, along with 4-port switches and Power over Ethernet devices. Each rest area has a dedicated equipment cabinet—installed by NJIT—that houses the pucks, cameras, and data transmission components.
We launched our first pilot site at the Harding rest area in 2021. That site features two microwave traffic sensors at the exit and entrance, nine CCTV cameras, and 44 pucks. In 2023, we expanded to the Deepwater rest area (also known as Carney’s Point), where we installed two traffic microwave sensors, one CCTV camera, and 68 pucks. All of this data feeds into a truck parking portal dashboard developed by NJIT to provide real-time insights. The dashboard displays the number of vehicles entering and exiting each site, average dwell time for trucks, the number of vehicles currently parked, and the occupancy status of individual parking spaces. It also tracks how long each spot has been occupied and provides historical usage statistics, including peak usage times.
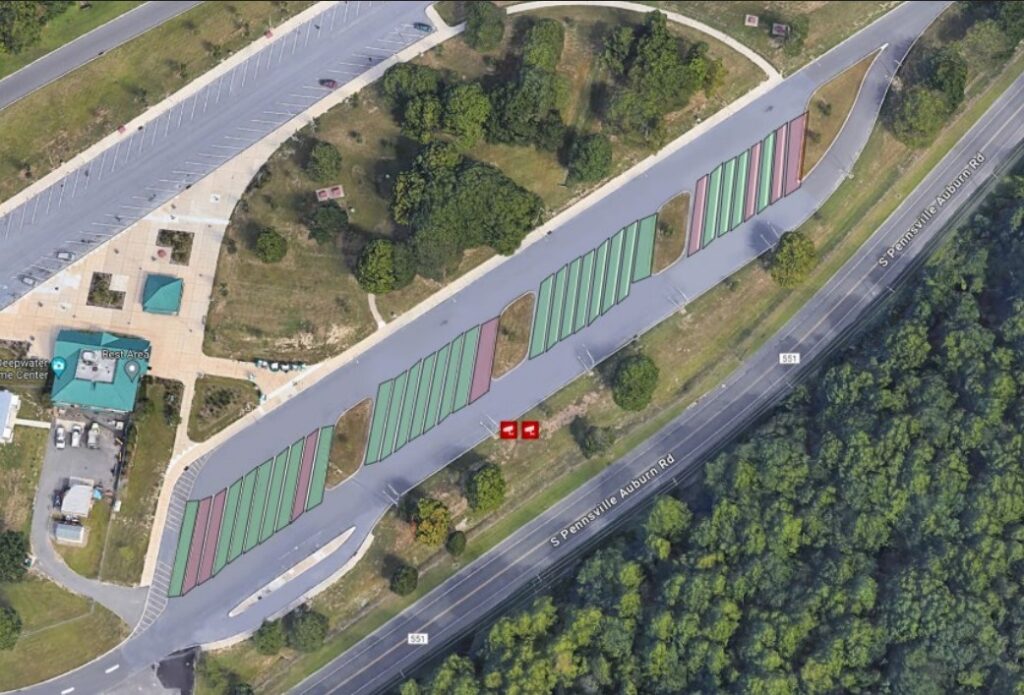
A virtual video wall offers live views of each rest area and shows how many trucks are currently parked and how many spaces remain available, based on the combined data sources. This is particularly valuable because truck parking demand is so high in New Jersey that drivers often end up parking at entrances, along curbs, or even perpendicular to marked spaces—creating unsafe conditions and occasionally blocking cameras.
To help address this, we have been working with NJIT to install two portable Dynamic Message Signs (DMS) near the Harding pilot site, located within five miles of the rest area on I-287 and I-78. These signs will display real-time parking availability.
More recently, we started the process of expanding the project to the Knowlton rest area. My team and I, along with NJIT, recently visited the site to begin the process of installing the necessary technologies.
Q. Are there any other projects or innovations that your or your team are working on that you would like to highlight?
A. Right now, we are focusing on expanding the existing projects we already have in place. In addition, we have started exploring virtual RWIS technology, which is still very new to us. It is currently in the early stages of development, so nothing has been substantiated yet.