UHPC for Bridge Preservation and Repair is a model innovation that was featured in FHWA’s Every Day Counts Program (EDC-6). UHPC is recognized as an innovative new material that can be used to extend the life of bridges. Its enhanced strength reduces the need for repairs, adding to the service life of a facility.
This Q&A article has been prepared following an interview with Jess Mendenhall and Samer Rabie of NJDOT, who provided an update on the pilot projects of UHPC around the state. The interview has been edited for clarity.
Q. While EDC-6 was underway, we spoke with your unit about the pilot projects being undertaken with UHPC. Some initial lessons were shared subsequently in a featured presentation given to the NJ STIC. Can you update us on results of those projects, and did they yield any benefits in the fields of safety or environmental considerations?
For the NJDOT Pilot Project, the thickness of the overlay was limited by the required depth for effectiveness, as well as the cost of the UHPC material and environmental permitting. To mitigate environmental permitting, we avoided any modifications to the existing elevations and geometry of the structure. Essentially, any removal of asphalt and concrete needed to be replaced to its original elevations.
UHPC overlays can significantly extend the service of bridge decks and even increase a structure’s capacity. Although safety improvements were not the primary objective of this application, there were rideability and surface drainage considerations in the design to enhance the conditions for the road users.
The environmental impacts of structural designs must be compared on the cradle-to-grave use cycle of the design at a project scale. Having a focus on sustainability is imperative; however, it is more meaningful when resiliency is also considered. While the greenhouse gas emissions of a volume of UHPC are higher than those of the same volume of concrete, UHPC enables the reduction in the amount of material required in structural designs and improves the durability of structures. Its exceptional compressive strength and toughness allow for the reduction of material usage. By minimizing maintenance requirements and extending the lifespan of infrastructure, UHPC reduces the consumption of materials, energy, and resources over time.
For example, we installed this overlay on 4 bridges as a preservation technique. Had we done nothing, they would have lasted approximately 10 more years. During that time they would have needed routine deck patching resulting in further contamination of the decks and in a condition that is no longer preservable and requires total deck replacement, with large volumes of concrete and much more environmental impact.
UHPC allowed us to take these decks that are still in decent shape and preserve them now with a relatively thin layer to make them exceed the service life of the superstructure and substructure.
Q. Has UHPC been incorporated into the design manual?
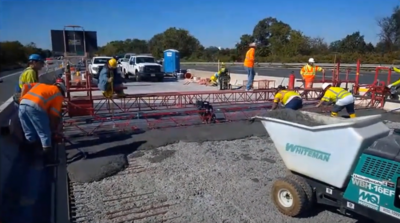
It is not in our current design manual, but we are working on the revised design manual. UHPC is presently being used for all closure pores between prefabricated components, overlays, and link-slabs. I don’t think we are ready to standardize it quite yet. We used it on the 4 bridges and it will continue to be used, but we will not standardize it until the industry is more predictable and we get more experience to develop thorough guidelines and specifications. It is incorporated into projects as a special provision with non-standard items.
Q. Have you been receiving more requests to use this technology from around the state?
It is much more commonly specified by designers or requested for use on many of our projects. We have responded to nationwide inquiries from state transportation agencies and universities seeking our specifications or input on specific testing and procedures.
Q. What efforts do you think can be taken to encourage more adoption amongst local agencies, counties, etc.?
We are keen on inviting the counties to any training or workshop that we are hosting as well as sharing our lessons learned thus far. I think they are aware of it.
Q. What kind of hurdles do you think exist that may limit widespread adoption?
It is possible that initial cost and industry experience with the material are still major limiting factors in adoption. We have also learned from specialty UHPC contractors that the innovation and availability of construction equipment geared for UHPC implementation are also lacking. Bringing into focus the life cycle costs and with more implementations, we think many of these hurdles will be overcome. Additionally, once UHPC is used more in routine maintenance the implementation would be more frequent and widespread; we know there is interest specifically in UHPC shotcrete once it is available.
Q. Are you familiar with any training, workshops, or conferences that have been done for staff or their partners on this topic?
We participated in the Accelerated Bridge Construction (ABC) conference in Miami, Florida, the International Bridge Conference (IBC) in Pittsburgh, Pennsylvania and the New York State DOT Peer Exchange. In Delaware, we presented at the Third International Interactive Symposium on UHPC. We also participated in the development of a UHPC course for the AASHTO Technical Training Solutions (TTS formerly TC3) which is now published on the AASHTO TTS portal and available on our LMS internally.
Q. Do you think there is any special training needed for the construction workforce to start using this technology?
Absolutely, the AASHTO TTS course and the EDC-6 workshops are geared towards the design and construction, TTS is more focused in the Construction. It’s an introduction to what to expect and how to implement it. UHPC is often used for repair projects, and many contractors may not have the experience or comfort with using the material.
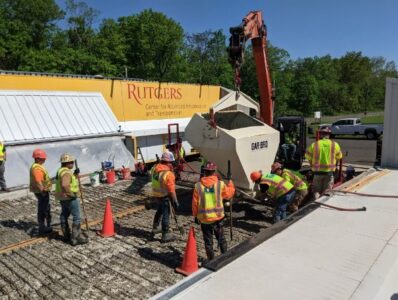
Q. What are the results of the pilot projects of UHPC?
This Pilot projects program demonstrated that UHPC overlays can be successfully placed on various structures, the work can be completed rapidly to minimize traffic impacts — we estimated roughly four weeks of traffic disruption per stage, and the benefits of UHPC can help preserve the existing infrastructure. Compared to deck replacement, UHPC overlays can rehabilitate a bridge deck at exceptional speeds with unique constructability and traffic patterns, as implemented in all four structures. However, limitations exist, and further research is necessary to investigate the issues identified in the pilot project, but the potential of this material outweighs the existing limitations.
Q. Has there been long-term testing data developed to gather performance data?
To assess the performance of the UHPC overlay, we put together a testing program to include NDT as well as physical sampling and lab testing. This objective will be accomplished by first establishing baseline conditions through an initial survey followed by periodic monitoring of the UHPC-overlaid bridges over succeeding years. This will help NJDOT assess the performance of UHPC as an overlay. Overall, the results show the overlay bond is performing well.
Q. Has the data from the pilot project been used to research further applications?
Further applications for UHPC overlay are on new bridge decks/superstructures, and the data from UHPC overlay research project are being used for these projects. There is an interest in header reconstruction with UHPC. If deck joints need to be replaced, they should be constructed with conventional HPC with UHPC at the surface to provide the same overlay protection over the entire structure. Also, self-consolidating and self-leveling UHPC was preferred for the full-depth UHPC header placement to ensure proper consolidation around tight corners and reinforcement. This will be further explored for maintenance operations as well.
For future projects, in lieu of full-depth header reconstruction in a single lift, a partial depth header removal and reconstruction or alternatively two lifts of header concrete should be evaluated to coincide with the deck overlay, in which case the benefits of the fast cure times from UHPC can still be realized. Two of the four bridges experienced air voids throughout the placement. A UHPC slurry with no
fibers was placed in the identified air voids; since the voids contained exposed fibers, they were considered to create adequate bonding with the UHPC slurry.
Update (June 2025):
Currently, NJDOT has not incorporated UHPC into the standard specifications, and no baseline document change has been issued to update the 2019 standard specifications to include UHPC. Due to rapid changes in the guide specifications, UHPC requirements are integrated into project documents as project specific special provisions, allowing for flexibility in updates. Future plans include incorporating UHPC into the standard specifications and issuing a baseline document change after the new draft bridge design manual is published.
NJDOT Special Provisions for UHPC Overlays
Resources
NJDOT Technology Transfer (2021, November). Stronger, More Resilient Bridges: Ultra High-Performance Concrete (UHPC) Applications in New Jersey. Interview with Pranav Lathia, Retrieved from: https://www.njdottechtransfer.net/2021/11/29/uhpc-stronger-more-resilient-bridges/
Mendenhall, Jess and Rabie, Samer. (2021, October 20). UHPC Overlays for Bridge Preservation—Lessons Learned. New Jersey Department of Transportation. https://www.njdottechtransfer.net/wp-content/uploads/2021/11/NJDOT-UHPC-Overlay-Research-Project-EDC-6-Workshop.pdf
New Jersey Department of Transportation. (2021, October 20). NJDOT Workshop Report. New Jersey Department of Transportation. https://www.njdottechtransfer.net/wp-content/uploads/2021/11/NJDOT-UHPC-Workshop-Final-Report.pdf
Rabie, Samer and Jess Mendenhall (2022, December). Design, Construction, and Evaluation of UHPC Bridge Deck Overlays for NJDOT. NJ STIC Presentation and Recording. Retrieved from: https://www.njdottechtransfer.net/2022/12/18/nj-stic-4th-quarter-2022-meeting/